PRODUCT INFORMATION
Spiral membrane is to make the flat membrane into sealed envelope-like membrane bags. Two membrane bags will be lined with a mesh spacing material in between , and tightly wounded on a porous center tube to form a membrane spiral. The spiral will be then placed into a circular pressure vessel. Feed stream flow into the membrane module from one end, which is the inlet, and keep flowing along with the axle. Under the pressure, the permeate will flow through the membrane along the radial to the central tube to export, the other end are the retained substances. Spiral membrane is divided into two types, one is material membrane, typically designed with the wide flow channel, are specifically for material separation; the other is water membrane, usually designed with the narrow flow channel, are dedicated to water treatment.
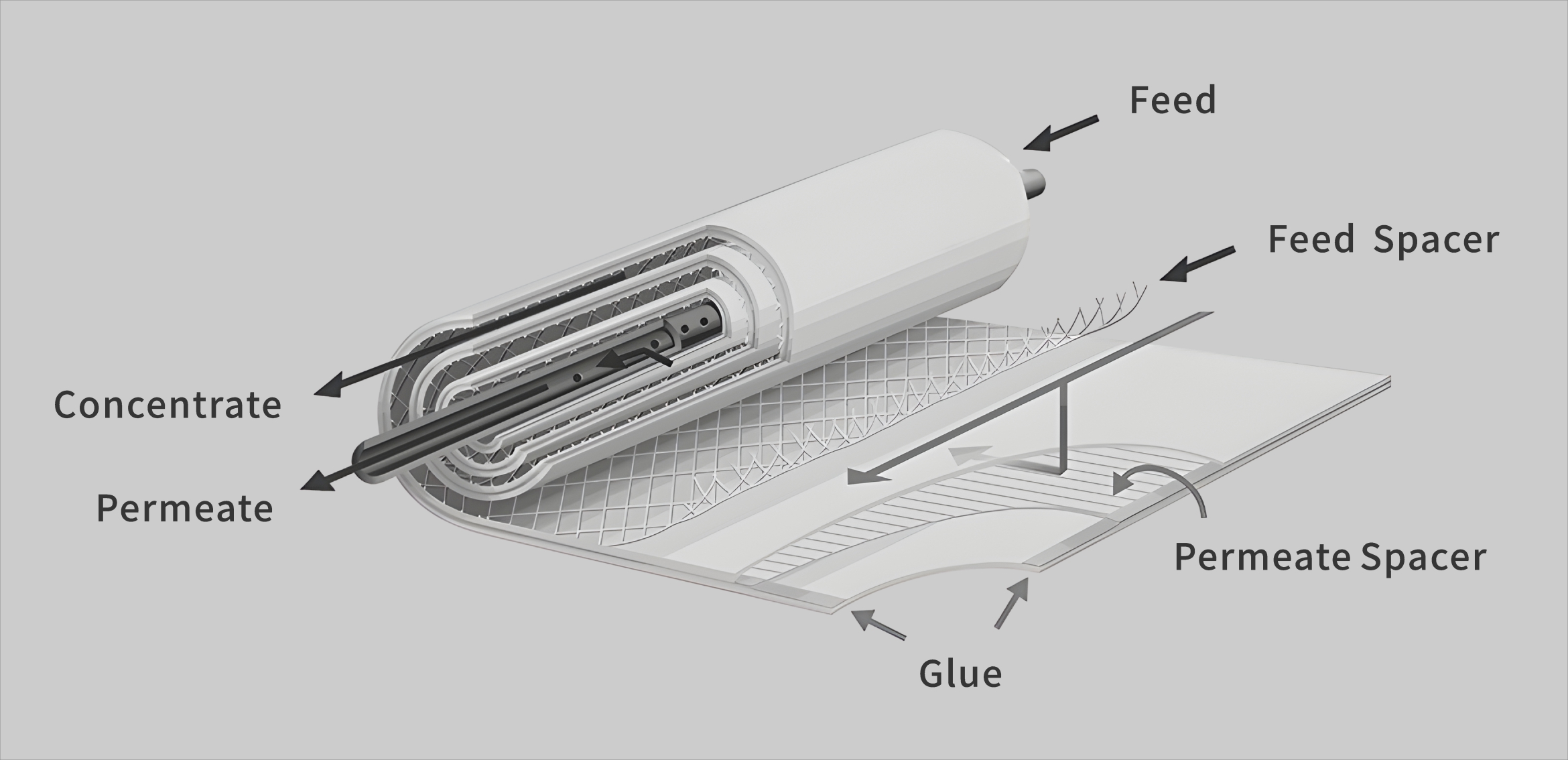
Advantages
Larger loading area Multiple feed flow channels
Stable and durable for long-term operation High pressure resistance
High tolerance to chemical solvent and temperature variation
PRODUCT INFORMATION
Spiral membrane is to make the flat membrane into sealed envelope-like membrane bags. Two membrane bags will be lined with a mesh spacing material in between , and tightly wounded on a porous center tube to form a membrane spiral. The spiral will be then placed into a circular pressure vessel. Feed stream flow into the membrane module from one end, which is the inlet, and keep flowing along with the axle. Under the pressure, the permeate will flow through the membrane along the radial to the central tube to export, the other end are the retained substances. Spiral membrane is divided into two types, one is material membrane, typically designed with the wide flow channel, are specifically for material separation; the other is water membrane, usually designed with the narrow flow channel, are dedicated to water treatment.
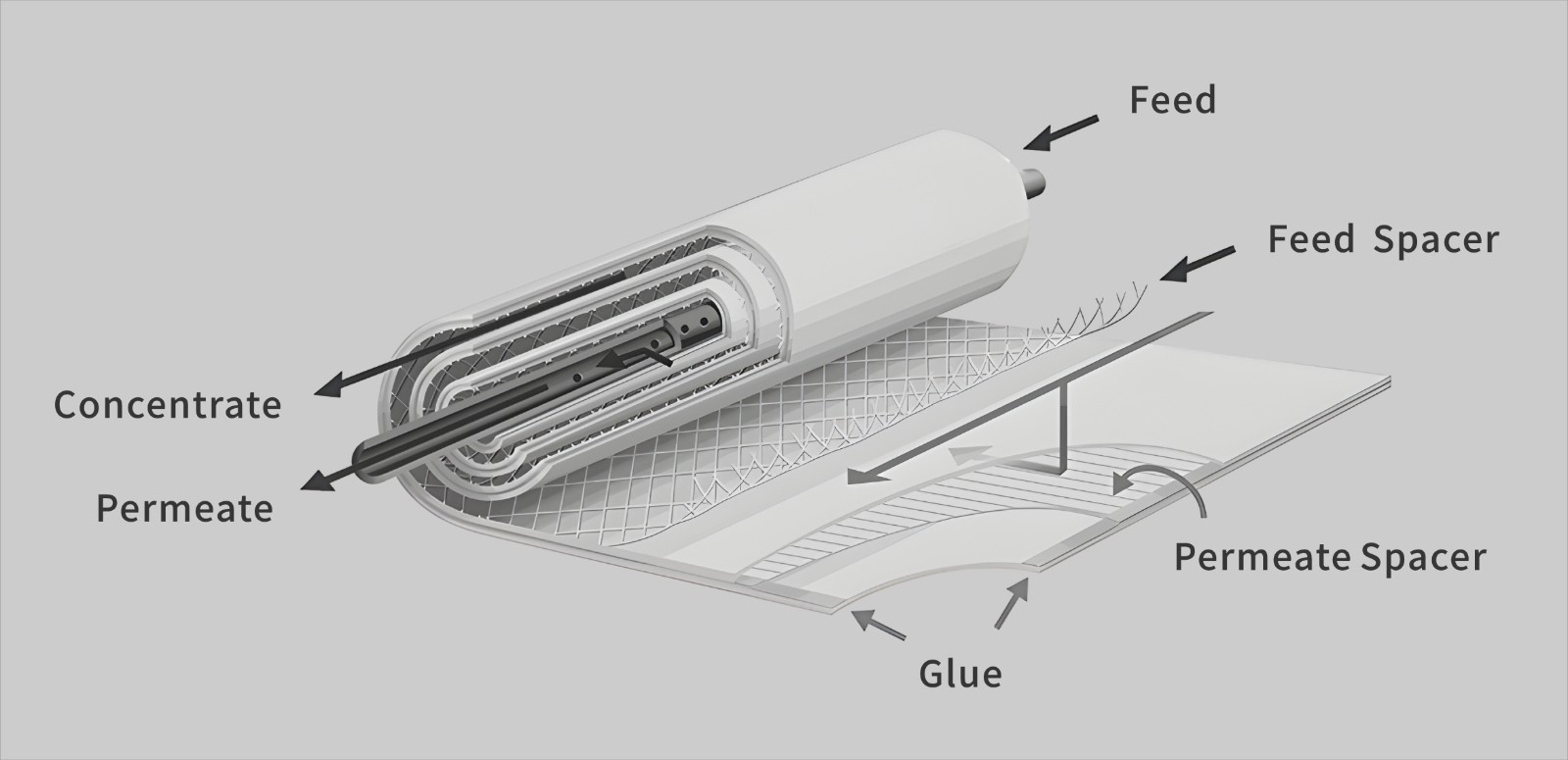
Advantages
1. Larger loading area
2. Multiple feed flow channels
3. Stable and durable for long-term operation
4. High pressure resistance
5. High tolerance to chemical solvent and temperature variation