Membrane fouling control and selection of membrane regeneration methods are very important for the application of membrane technology, as well as for organic tubular membrane technology. The factors of membrane fouling mainly include the characteristics of the membrane itself ( such as membrane pore size and distribution, membrane structure, physical characteristics of the membrane, interaction among membrane, solute and solvent ) and membrane module, influent water quality, feed material properties and operating conditions. In practical application, membrane fouling control methods are different for different separation systems.
1. Pretreatment of Feed Material
Preteat the feed material to meet the inlet water standard of the membrane module. In order to reduce membrane fouling, it is necessary to determine the appropriate pretreatment method first, and the appropriate pretreatment is helpful to reduce membrane fouling, improve permeability flux and membrane retention performance. Physical treatment usually includes pre-filtration and centrifugation to remove suspended particles that may clog membrane pores; Chemical treatment involves adjusting the pH of the feed material to keep macromolecules or colloidal contaminants away from the isoelectric point to reduce the tendency to form gel layers. For example, for proteins, the regulation of pH is important. In this case, fouling is minimal when the pH corresponds to the isoelectric point of the protein, that is, when the protein is electrically neutral. The pretreatment of the feed material must consider the characteristics of the material itself, and chemical pretreatment can not be carried out for the material whose performance can not be changed.
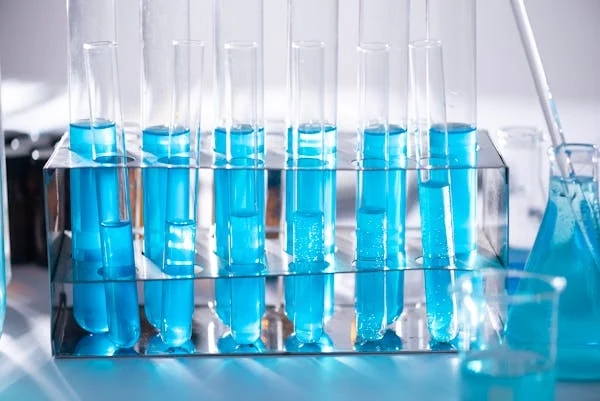
2. Optimize the Properties of the Membrane
Changing the properties of membrane can effectively reduce membrane fouling, so the research on the modification and anti-fouling properties of membrane materials has been a hot topic in academia and industry. The fouling of porous membrane (such as microfiltration membrane and ultrafiltration membrane) is generally much heavier than that of dense membrane. The narrow membrane aperture distribution helps to reduce fouling. The use of hydrophilic membrane can help reduce fouling, and the general protein is more easily adsorbed and difficult to remove on the hydrophobic membrane than on the surface of the hydrophilic membrane. The use of a (negative) electric membrane is also conducive to reducing membrane fouling, especially when the feed material contains (negative) electric particles.
The hydrophilic modification of membrane can be divided into physical modification and chemical modification. The physical modification includes co-mixing the surface layer. “Co-mixing” is to mix the hydrophilic polymers with membrane forming materials to improve the hydrophilicity of the membrane. By chemical modification, hydrophilic block copolymers can be added into organic polymer membrane forming materials to obtain hydrophilic membrane and improve the fouling resistance of the membrane. Surface coating refers to the formation of a functional pre-coating layer on the surface of the membrane to prevent the adsorption of the membrane material and the components in the feed material, so as to improve the fouling resistance of the separation membrane.
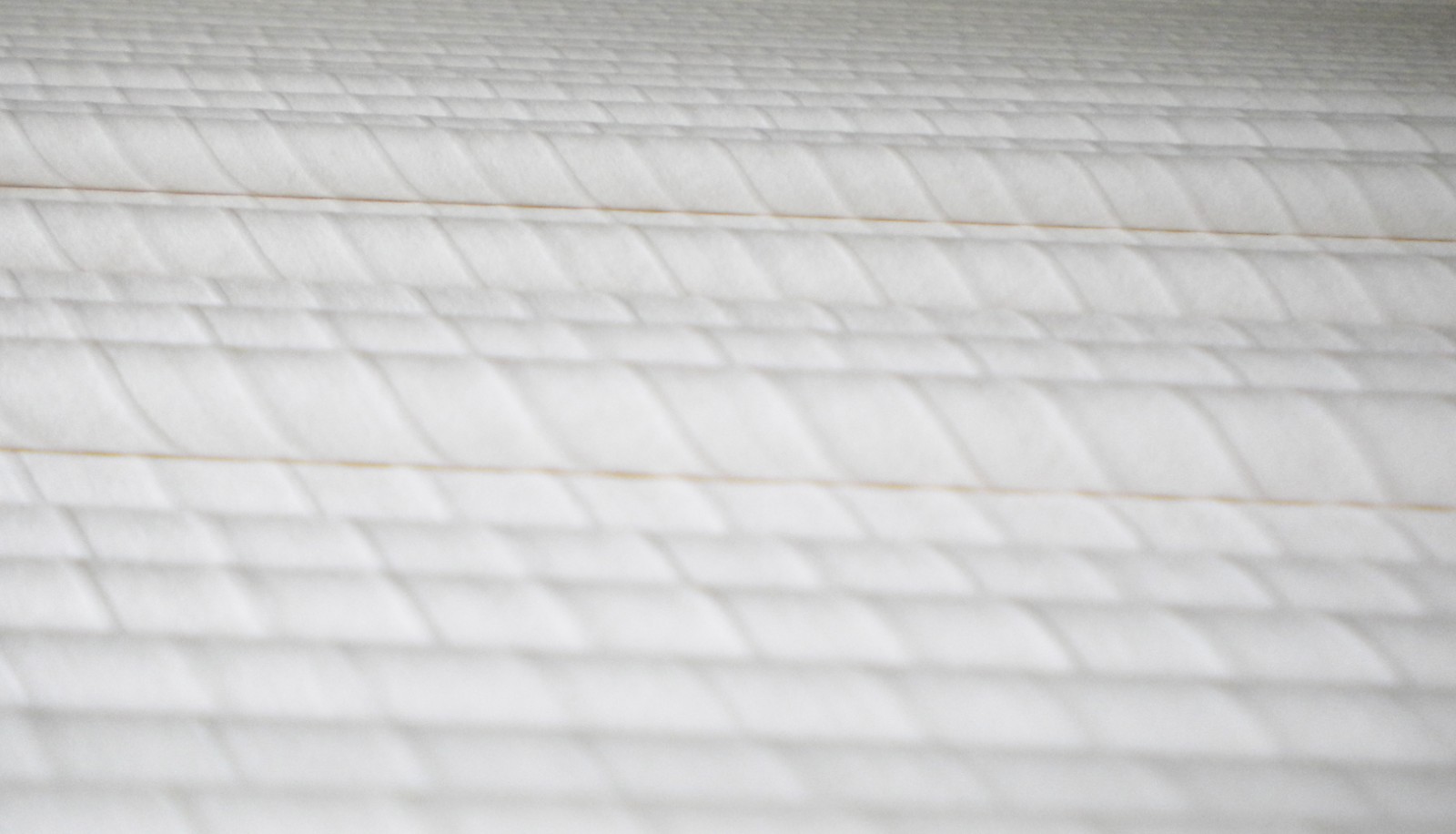
3. Operating Parameter
Operating parameters include feed flow rate, pressure and temperature. Generally, high feed flow rate can reduce the concentration polarization or the formation of sedimentary layer, and improve the water permeability. However, to consider that some biological products are sensitive to shear force, it is necessary to choose the appropriate feed flow rate. In the case of concentration polarization phenomenon is not serious, it is usually possible to increase the pressure to improve the permeability, but the test is needed to determine its limit, because increasing the pressure will increase the concentration polarization and membrane fouling, and the "gel layer" will be formed after the critical pressure, and the water permeability will no longer increase with the pressure. Therefore, the operating pressure should be appropriate to not exceed the critical pressure. Temperature usually has an effect on water permeability by affecting the viscosity of the feed material. However, when considering the temperature rise, it is necessary to pay attention to the stability of the activity of biological products and the solubility of some proteins with the change of temperature, otherwise the temperature rise sometimes reduces the water permeability.
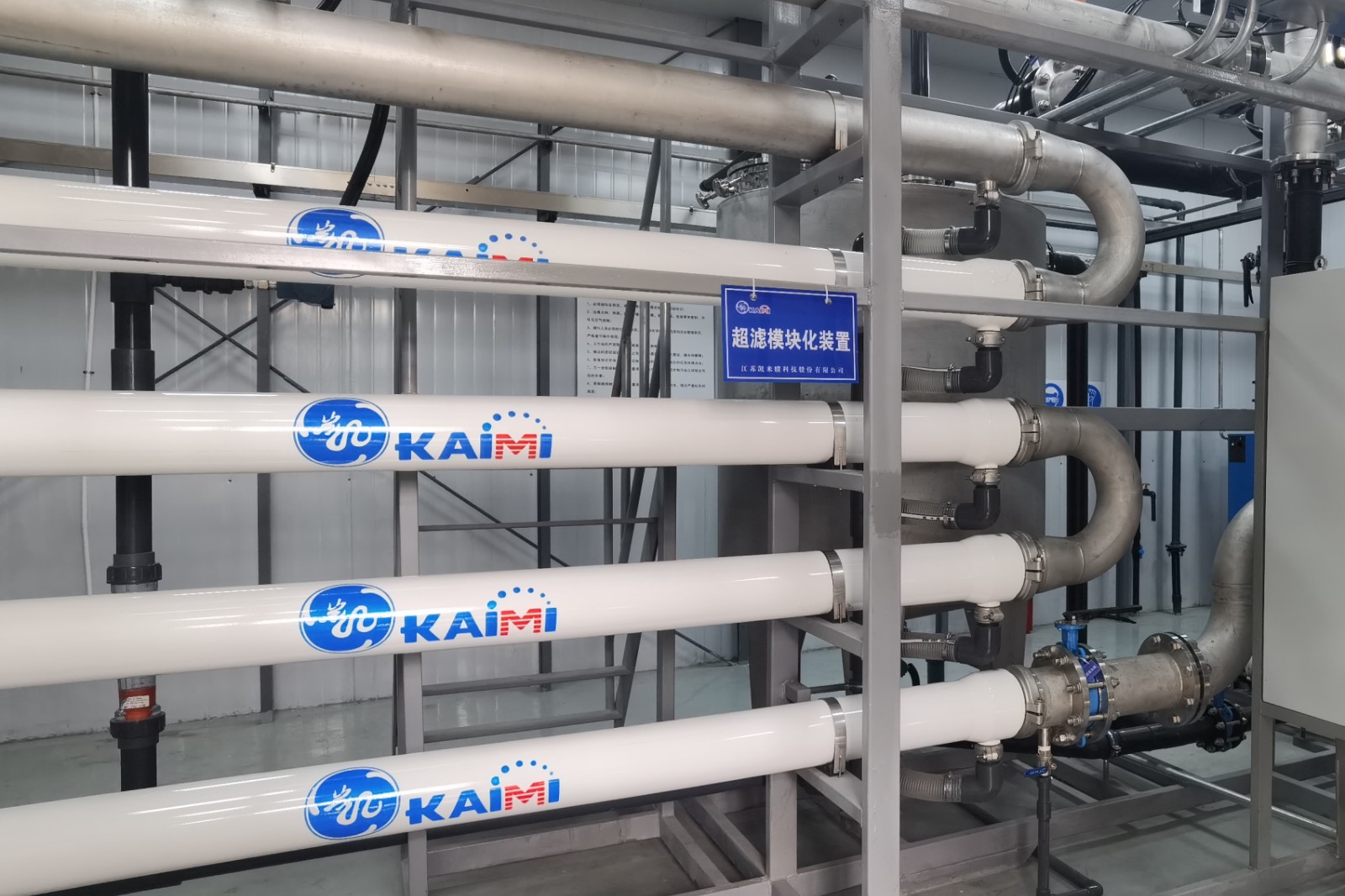
4. Selection of Membrane Pore Size or Molecular Weight Cut-off (MWCO)
Theoretically speaking, on the premise of ensuring that the required particles or macromolecular solutes can be retained, the membrane with a larger pore size or MWCO should be selected as far as possible to obtain a higher water permeability. However, the actual experiment found that the selection of larger membrane pore size, because of the higher fouling rate, the long-term water permeability decreased. This is because when the size of the substance to be separated is similar to the membrane pore size, due to the effect of pressure, when the solvent passes through the membrane, the particles are brought to the membrane surface, which is easy to cause blockage. When membrane pore size is smaller than the particle or solute size, it is difficult for them to stay and aggregate on the surface of the membrane due to the action of cross-flow, so it is not easy to clog.
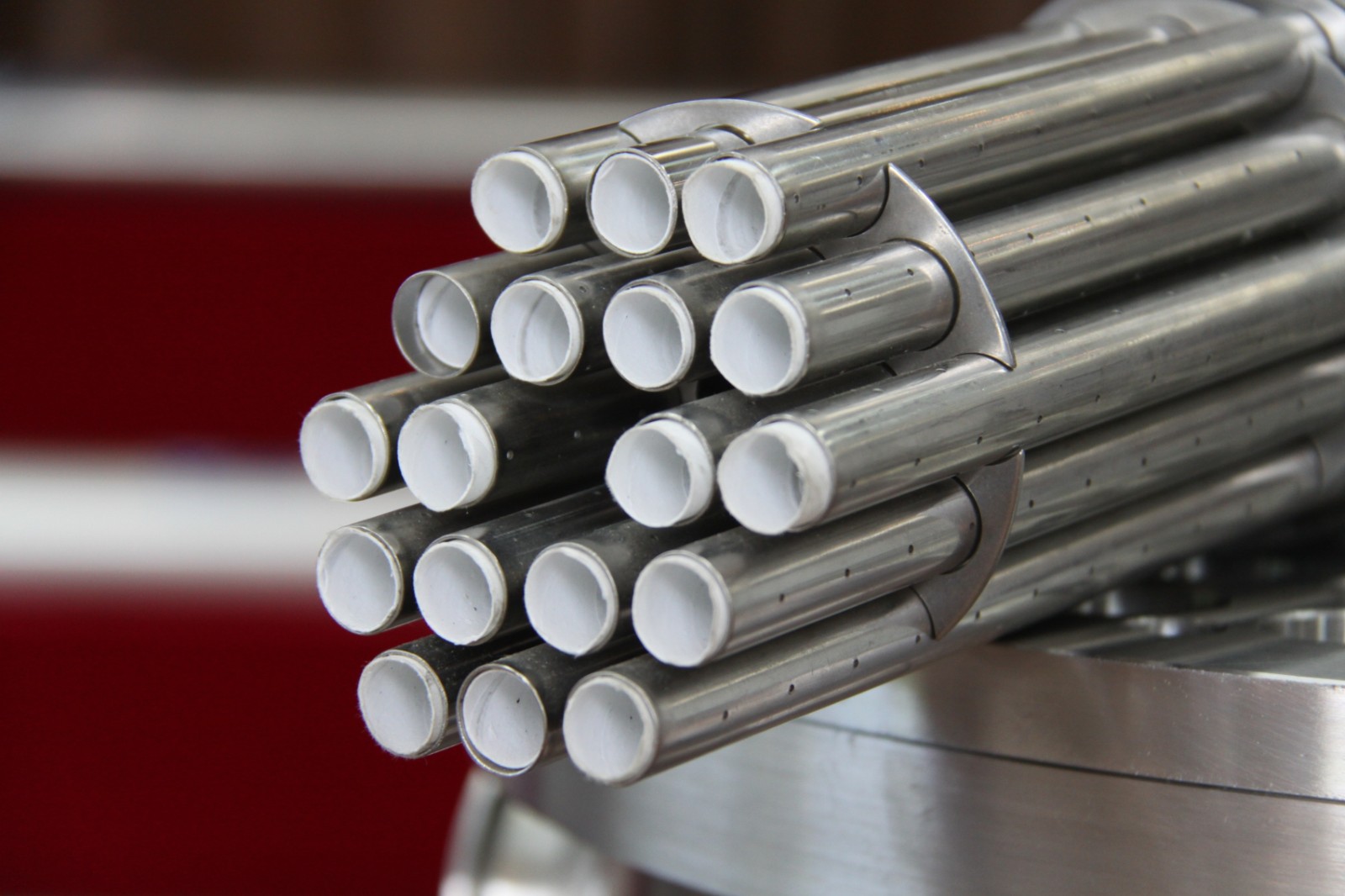
5. Selection of Membrane Structure
The choice of membrane structure against fouling is also very important. For microfiltration membranes, the symmetrical structure is obviously more likely to clog than the asymmetric structure, because the surface opening of the curved pore size of the symmetrical structure is sometimes larger than the internal aperture, so that particles entering the surface are often trapped in the membrane. In the asymmetric structure of the microfiltration membrane, the particles are basically retained on the surface, not easily to clog in the membrane, easy to be carried away by cross-flow. Even if there is accumulation and blockage on the surface of the membrane, it can be easily washed away by backwashing.
6. Salt Effect
Inorganic salts may also have a significant impact on membrane fouling. Some inorganic salt complexes will sediment directly on the surface of the membrane or in the membrane pore, or increase the adsorption amount of protein on the membrane and contaminate the membrane. Some inorganic salts also change the ionic strength of the solution, affecting the solubility, configuration and suspension state of the protein, so that the density of the sedimentary layer formed by it changes, thus affecting the filtration resistance of the membrane, and ultimately leading to the change of the membrane flux. However, the effect of inorganic salts on membrane fouling is related to the chemical properties of the membrane, the properties of the protein to be separated and the pH of the feed material, which should be comprehensively considered.
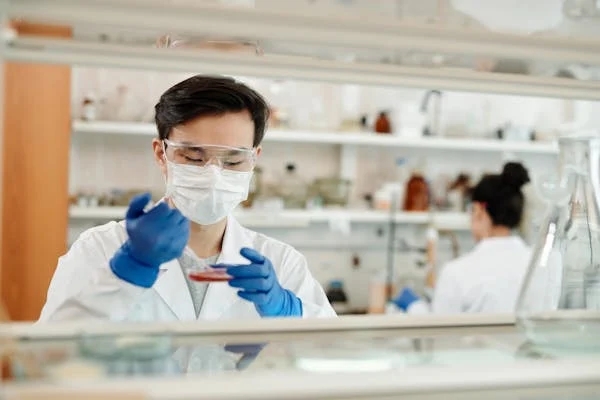
Membrane fouling control and selection of membrane regeneration methods are very important for the application of membrane technology, as well as for organic tubular membrane technology. The factors of membrane fouling mainly include the characteristics of the membrane itself ( such as membrane pore size and distribution, membrane structure, physical characteristics of the membrane, interaction among membrane, solute and solvent ) and membrane module, influent water quality, feed material properties and operating conditions. In practical application, membrane fouling control methods are different for different separation systems.
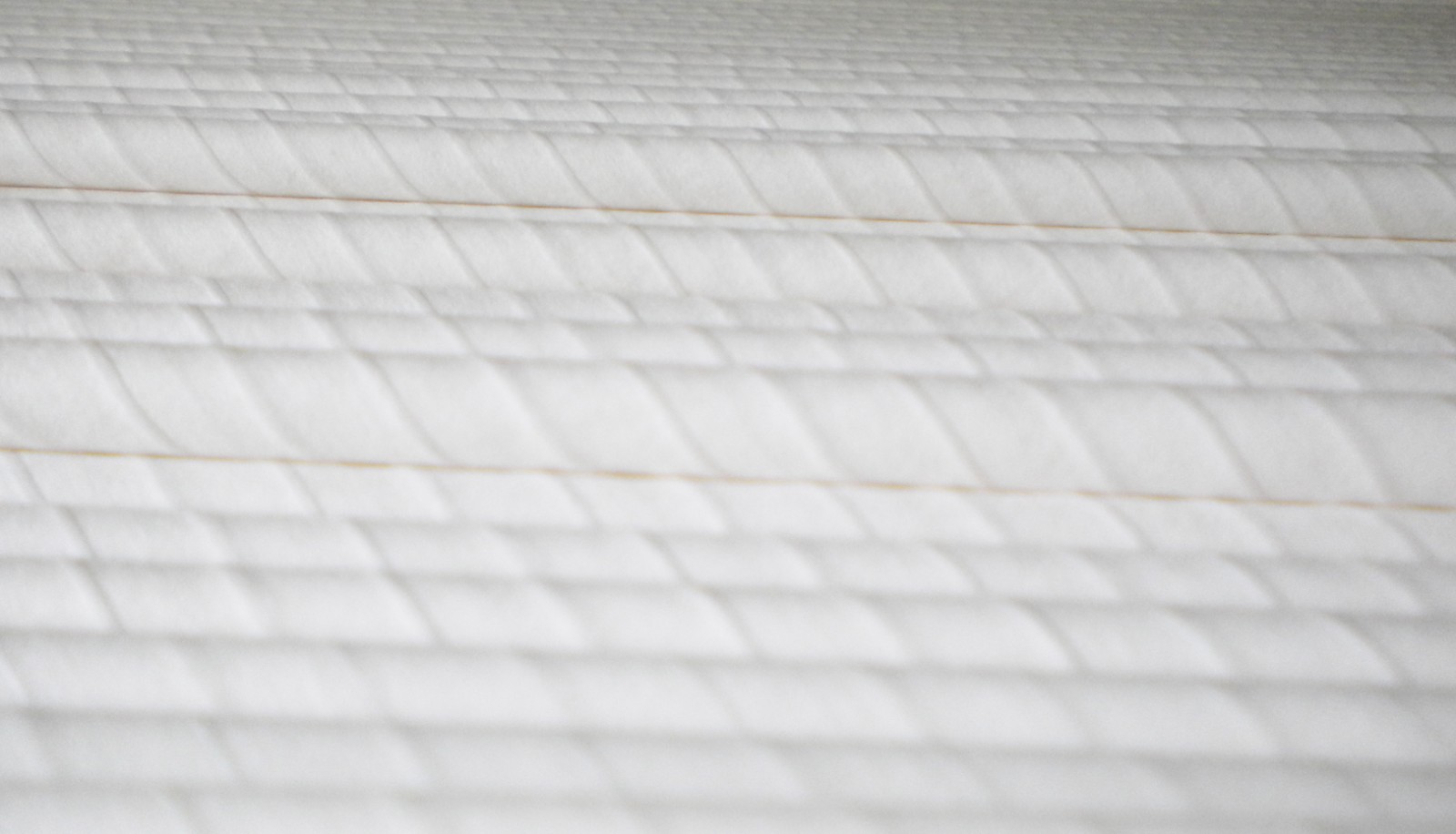
1. Pretreatment of Feed Material
Preteat the feed material to meet the inlet water standard of the membrane module. In order to reduce membrane fouling, it is necessary to determine the appropriate pretreatment method first, and the appropriate pretreatment is helpful to reduce membrane fouling, improve permeability flux and membrane retention performance. Physical treatment usually includes pre-filtration and centrifugation to remove suspended particles that may clog membrane pores; Chemical treatment involves adjusting the pH of the feed material to keep macromolecules or colloidal contaminants away from the isoelectric point to reduce the tendency to form gel layers. For example, for proteins, the regulation of pH is important. In this case, fouling is minimal when the pH corresponds to the isoelectric point of the protein, that is, when the protein is electrically neutral. The pretreatment of the feed material must consider the characteristics of the material itself, and chemical pretreatment can not be carried out for the material whose performance can not be changed.
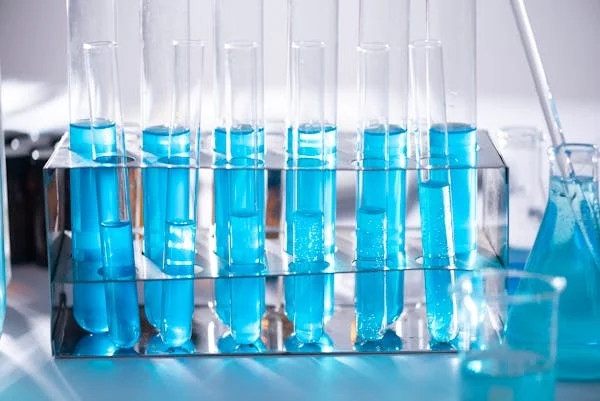
2. Optimize the Properties of the Membrane
Changing the properties of membrane can effectively reduce membrane fouling, so the research on the modification and anti-fouling properties of membrane materials has been a hot topic in academia and industry. The fouling of porous membrane (such as microfiltration membrane and ultrafiltration membrane) is generally much heavier than that of dense membrane. The narrow membrane aperture distribution helps to reduce fouling. The use of hydrophilic membrane can help reduce fouling, and the general protein is more easily adsorbed and difficult to remove on the hydrophobic membrane than on the surface of the hydrophilic membrane. The use of a (negative) electric membrane is also conducive to reducing membrane fouling, especially when the feed material contains (negative) electric particles.
The hydrophilic modification of membrane can be divided into physical modification and chemical modification. The physical modification includes co-mixing the surface layer. “Co-mixing” is to mix the hydrophilic polymers with membrane forming materials to improve the hydrophilicity of the membrane. By chemical modification, hydrophilic block copolymers can be added into organic polymer membrane forming materials to obtain hydrophilic membrane and improve the fouling resistance of the membrane. Surface coating refers to the formation of a functional pre-coating layer on the surface of the membrane to prevent the adsorption of the membrane material and the components in the feed material, so as to improve the fouling resistance of the separation membrane.
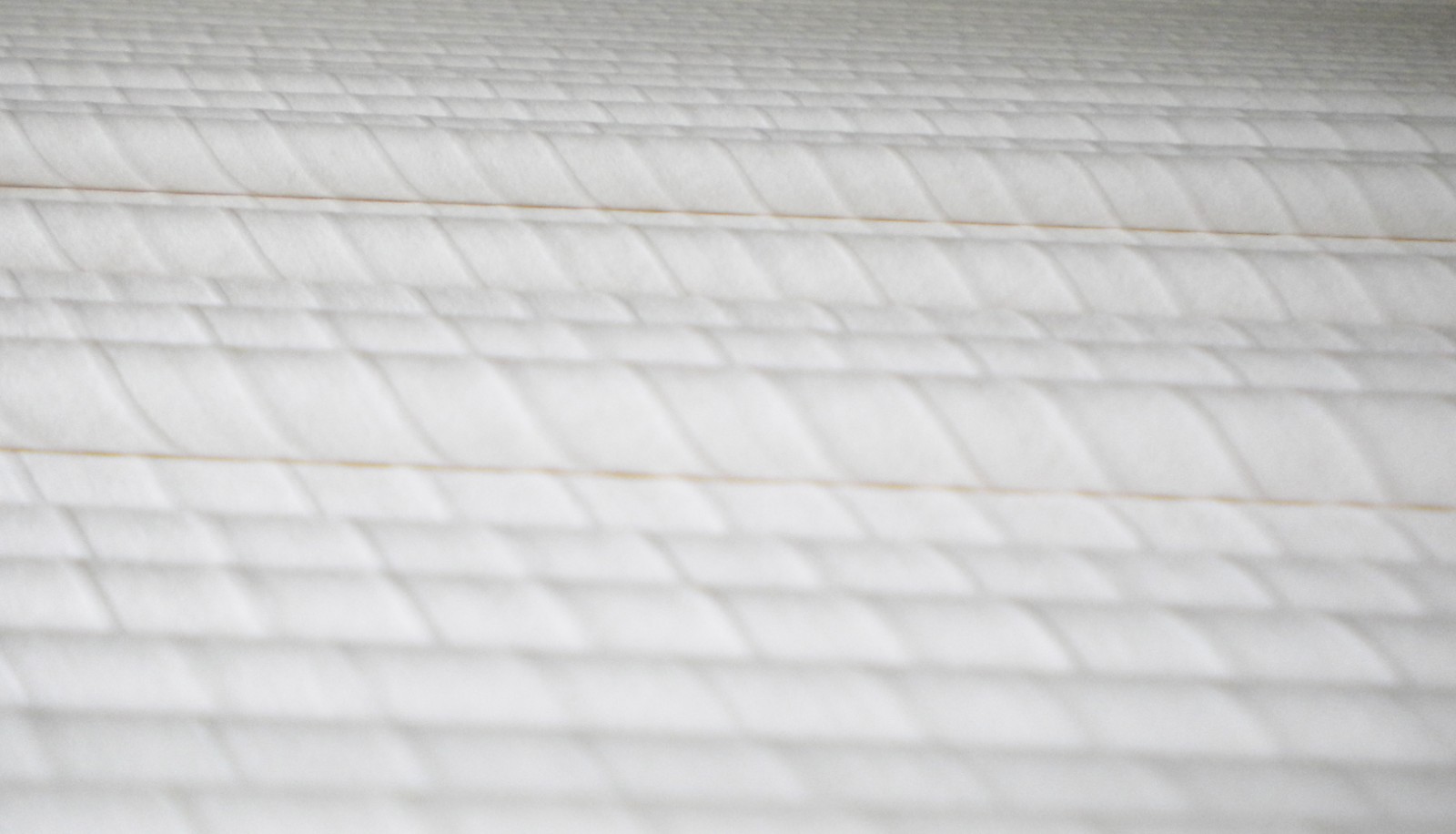
3. Operating Parameter
Operating parameters include feed flow rate, pressure and temperature. Generally, high feed flow rate can reduce the concentration polarization or the formation of sedimentary layer, and improve the water permeability. However, to consider that some biological products are sensitive to shear force, it is necessary to choose the appropriate feed flow rate. In the case of concentration polarization phenomenon is not serious, it is usually possible to increase the pressure to improve the permeability, but the test is needed to determine its limit, because increasing the pressure will increase the concentration polarization and membrane fouling, and the "gel layer" will be formed after the critical pressure, and the water permeability will no longer increase with the pressure. Therefore, the operating pressure should be appropriate to not exceed the critical pressure. Temperature usually has an effect on water permeability by affecting the viscosity of the feed material. However, when considering the temperature rise, it is necessary to pay attention to the stability of the activity of biological products and the solubility of some proteins with the change of temperature, otherwise the temperature rise sometimes reduces the water permeability.
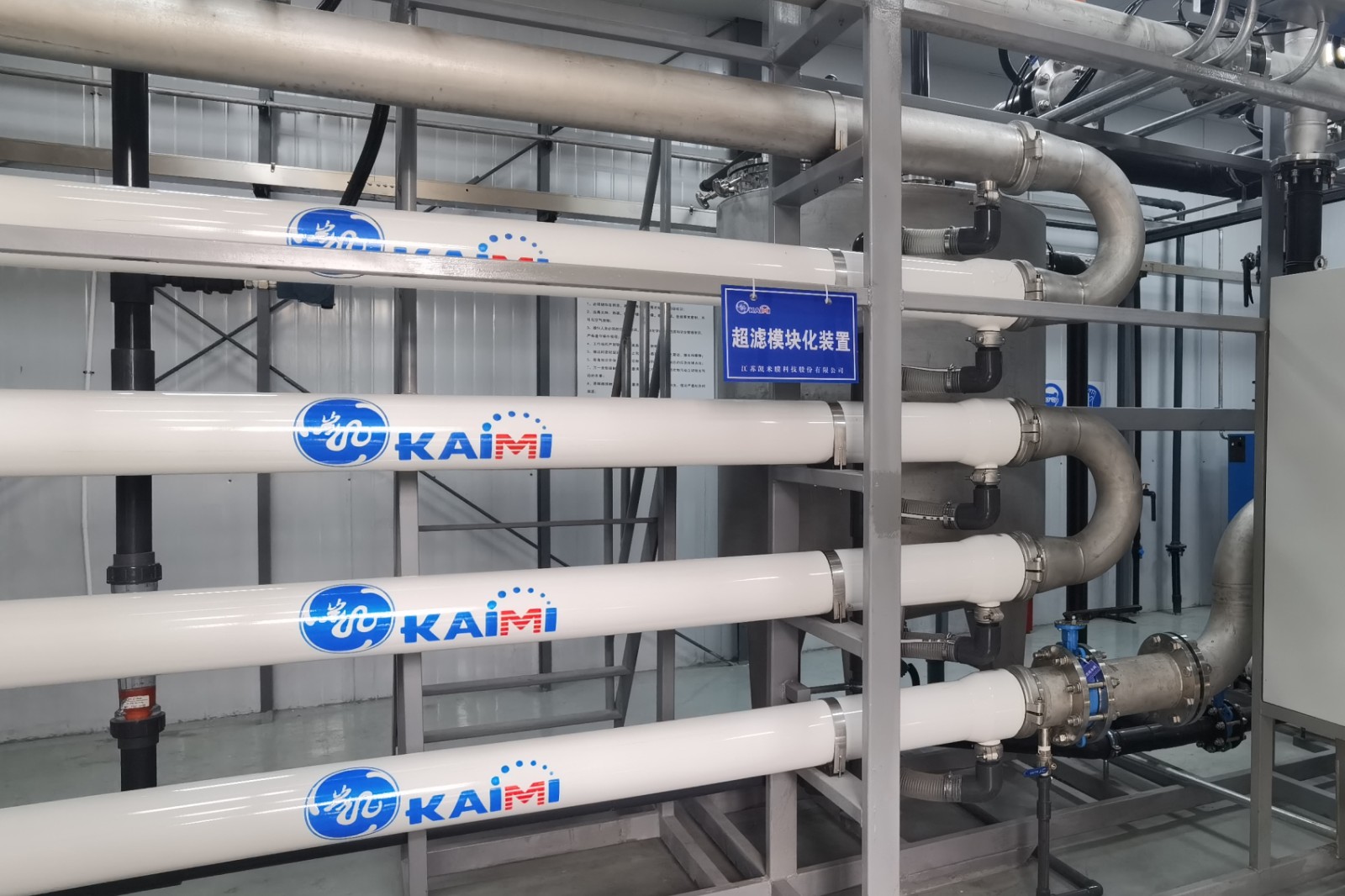
4. Selection of Membrane Pore Size or Molecular Weight Cut-off (MWCO)
Theoretically speaking, on the premise of ensuring that the required particles or macromolecular solutes can be retained, the membrane with a larger pore size or MWCO should be selected as far as possible to obtain a higher water permeability. However, the actual experiment found that the selection of larger membrane pore size, because of the higher fouling rate, the long-term water permeability decreased. This is because when the size of the substance to be separated is similar to the membrane pore size, due to the effect of pressure, when the solvent passes through the membrane, the particles are brought to the membrane surface, which is easy to cause blockage. When membrane pore size is smaller than the particle or solute size, it is difficult for them to stay and aggregate on the surface of the membrane due to the action of cross-flow, so it is not easy to clog.
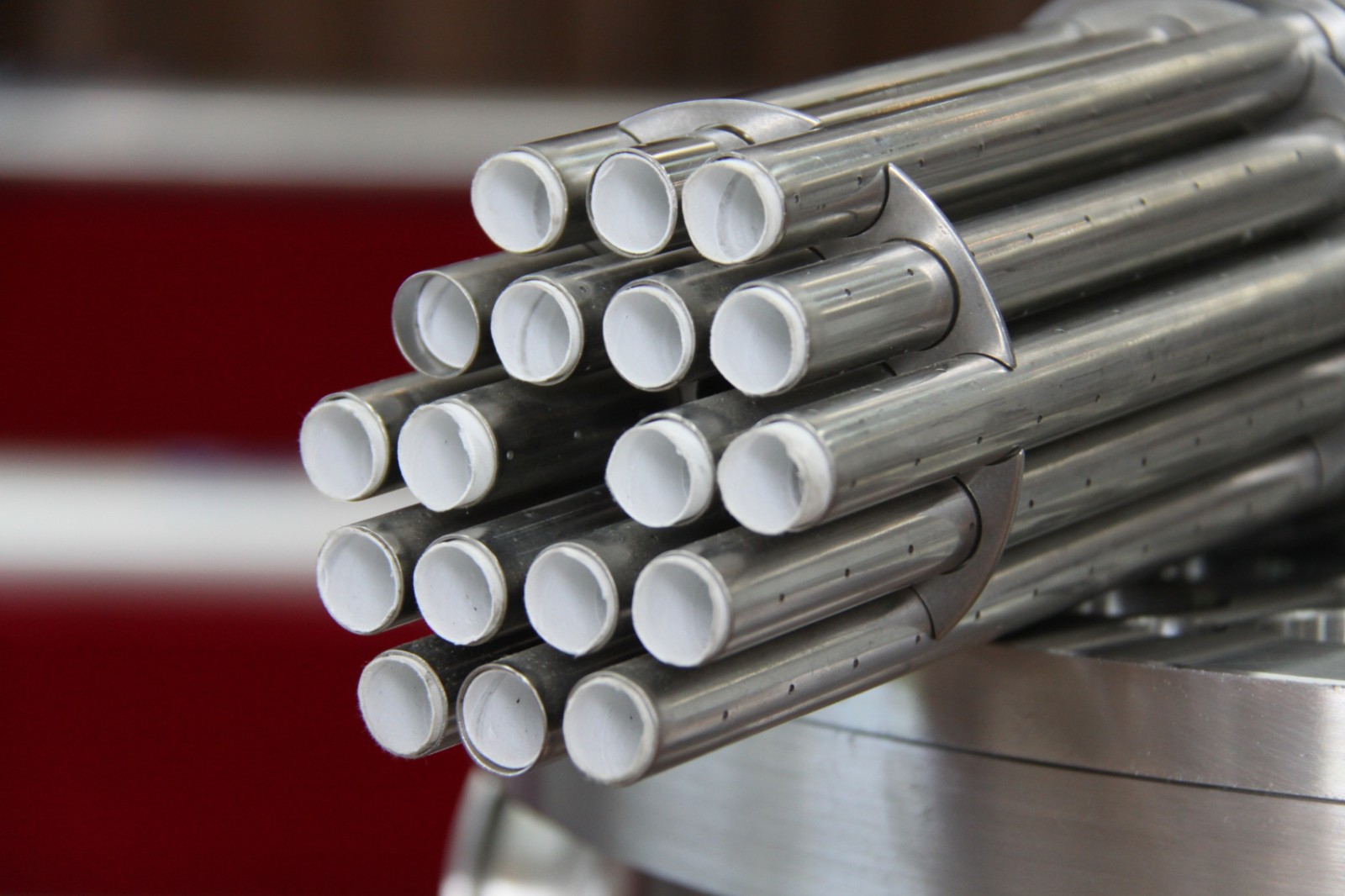
5. Selection of Membrane Structure
The choice of membrane structure against fouling is also very important. For microfiltration membranes, the symmetrical structure is obviously more likely to clog than the asymmetric structure, because the surface opening of the curved pore size of the symmetrical structure is sometimes larger than the internal aperture, so that particles entering the surface are often trapped in the membrane. In the asymmetric structure of the microfiltration membrane, the particles are basically retained on the surface, not easily to clog in the membrane, easy to be carried away by cross-flow. Even if there is accumulation and blockage on the surface of the membrane, it can be easily washed away by backwashing.
6. Salt Effect
Inorganic salts may also have a significant impact on membrane fouling. Some inorganic salt complexes will sediment directly on the surface of the membrane or in the membrane pore, or increase the adsorption amount of protein on the membrane and contaminate the membrane. Some inorganic salts also change the ionic strength of the solution, affecting the solubility, configuration and suspension state of the protein, so that the density of the sedimentary layer formed by it changes, thus affecting the filtration resistance of the membrane, and ultimately leading to the change of the membrane flux. However, the effect of inorganic salts on membrane fouling is related to the chemical properties of the membrane, the properties of the protein to be separated and the pH of the feed material, which should be comprehensively considered.
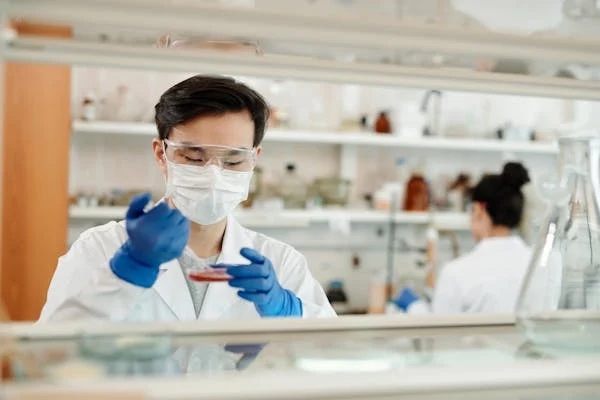